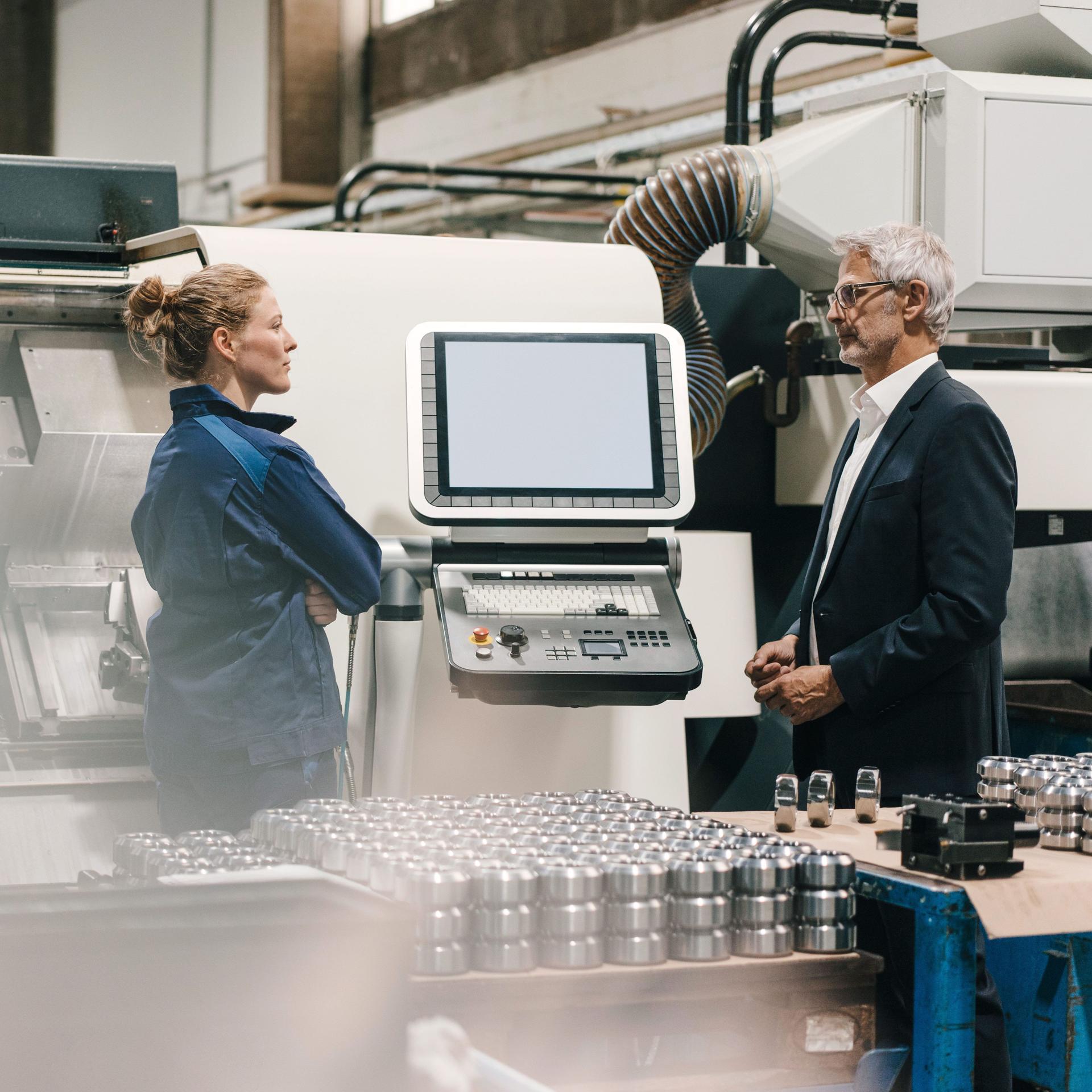
Im Zuge der digitalen Transformation führen Unternehmen neue Technologien ein, verändern Geschäftsmodelle und Prozesse. Der Wandel zur Industrie 4.0 ist in vollem Gange. Über 90 Prozent der Betriebe sehen ihn laut BMWK-Umfrage als Voraussetzung dafür, dass die deutsche Industrie wettbewerbsfähig bleiben kann.
Industrie 4.0 bezeichnet die zunehmende digitale Vernetzung von Abläufen und Maschinen oder Geräten beziehungsweise Produkten in der Wirtschaft.
Dadurch entstehen zahlreiche neue Möglichkeiten, Prozesse zu optimieren, effizienter zu werden, Menschen zu entlasten und Daten zu generieren.
Bei der Finanzierung neuer digitaler Technologien können Unternehmen unter Umständen auf Fördermittel des Bundes zurückgreifen.
Eine Vielzahl neuer Möglichkeiten
Industrie 4.0 bringt über alle Branchen hinweg Veränderungen mit sich. Welche Bereiche und Maßnahmen dabei im Einzelnen sinnvoll sein können, ist ganz unterschiedlich. Ein paar Beispiele:
- Produktionsabläufe digital vernetzen: Mit neuen Technologien ist es möglich, die Produktion komplett zu digitalisieren und die Abläufe optimal aufeinander abzustimmen.
- Vernetzte Produkte: Smarte Produkte stehen selbst in Kommunikation mit den digitalen Abläufen oder dem Produzenten. Sie können Daten senden, um effizienter herzustellen, zu verbessern oder frühzeitig zu warten.
- Vernetzte Maschinen: Selbstlernende und miteinander vernetzte Maschinen können die eigene Reparatur oder das Nachfüllen von Materialien veranlassen – die zunehmende Automatisierung sorgt für einen reibungsloseren Ablauf.
- Datengenerierung: Die vernetzten Produkte können über den gesamten Herstellungsprozess bis hin zum Kunden oder der Kundin Daten sammeln. Diese können wiederum so analysiert werden, dass sie Optimierungen und neuen Technologien den Weg bereiten.
Mögliche Folgen der industriellen Veränderungen
Keine Frage: Die Arbeitswelt verändert sich durch die Industrie 4.0 entscheidend. Dieser Prozess ist bereits voll im Gange. Menschen werden immer enger mit Maschinen zusammenarbeiten. Arbeitsplätze, die automatisiert werden können, fallen vermehrt weg. Stattdessen werden neue Facharbeitsplätze entstehen. Mitarbeiterinnen und Mitarbeiter müssen für neue Technologien geschult werden. Innovationen sind gefragt.
Laut Angaben des BMWK gehen drei Viertel der Industrieunternehmen davon aus, dass Industrie 4.0 den CO2-Ausstoß verringern wird. Durch die neuen Technologien wird es vielen Arbeitnehmerinnen und Arbeitnehmern je nach Arbeitsstelle beispielsweise möglich sein, im Homeoffice zu arbeiten. Ressourcen werden aber auch dadurch geschont, dass Abläufe effizienter werden. Ganze 95 Prozent der Industrieunternehmen sehen laut BMWK Industrie 4.0 als Chance.
Tipp: Mehr Informationen finden Sie auf der Plattform Industrie 4.0.
Herausforderung für Mittelständler
Das größte Hindernis für Industrie-4.0-Projekte sind laut Bitkom-Umfrage die Investitionskosten. 81 Prozent der Befragten gaben dies als Grund für ihre Zurückhaltung bei der Einführung von Industrie-4.0-Technologien an.
Zu kurz gedacht, sagt Winfried Holz, Mitglied des Bitkom-Präsidiums: „Wer seine Produktion fit machen will für die Zukunft, muss in aller Regel erst einmal investieren. Diese Investitionen sind aber genauso essenziell wie die Pflege und Wartung von Maschinen.“ Seine Schlussfolgerung: „Ohne diese Investitionen wird es künftig keine moderne, effiziente Produktion mehr geben.“
Förderungen: Bund und Kreditinstitute helfen mit
Zudem müssen mittelständische Unternehmen die Kosten nicht allein stemmen. Neben Programmen des Bundes und der Länder gibt es zahlreiche andere Förderungen, die Sparkassen und Banken ihren Kundinnen und Kunden vermitteln. Sie werden rege genutzt.
Ohne die Unterstützung von Expertinnen und Experten ist es aber für den einzelnen Unternehmer oder die einzelne Unternehmerin nahezu unmöglich, sich im Dschungel der vielfältigen Fördermöglichkeiten zurechtzufinden.
Die Förderung eines Industrie-4.0-Projekts hängt beispielsweise davon ab, in welcher Phase es sich befindet. Für ein Projekt, das sich in der Forschungs- und Entwicklungsphase befindet, stehen andere Förderprogramme zur Verfügung als für ein Projekt in der Umsetzung. Davon sollten sich Betriebe jedoch nicht abschrecken lassen. Denn die Sparkassen und Landesbanken helfen Unternehmerinnen und Unternehmern dabei, ihre Firmen fit für die Zukunft zu machen. Gerne beraten wir auch über alle möglichen Fördermittel.
Sie möchten in neue Technologien investieren?
Häufige Fragen zu Industrie 4.0
Der Begriff meint den Prozess der zunehmenden digitalen Vernetzung von Abläufen, Maschinen und Produkten in der Wirtschaft. Dabei spielen beispielsweise das Internet der Dinge und Maschine-zu-Maschine-Kommunikation eine zentrale Rolle. Intelligente und selbstlernende Systeme verändern die Arbeitswelt.
Die Zahl 4.0 deutet dabei an, dass diese neue Form der Digitalisierung der Produktion die Wirtschaft so gravierend umgestalten wird, dass nach den bisherigen drei industriellen Revolutionen von einer vierten Revolution gesprochen werden kann. Mit der Industrie 4.0 würde also eine neue Epoche eingeleitet. Das „Punkt 0“ nach der Industrie 4 fungiert als Anlehnung an die Bezeichnungen von Software-Produkten.
Der Begriff wurde öffentlich erstmals 2011 verwendet. In der Folge wurden an verschiedenen Stellen Konzepte zur Umsetzung erarbeitet. Die „Plattform Industrie 4.0“ zur Förderung der Industrie 4.0 wurde 2013 gemeinsam vom Branchenverband der deutschen Informations- und Telekommunikationsbranche (Bitkom), dem Verband Deutscher Maschinen- und Anlagenbau (VDMA) und dem Verband der Elektro- und Digitalindustrie (ZVEI) gegründet. Aktuell wird sie vom Bundesministerium für Wirtschaft und Klimaschutz (BMWK) und dem Bundesministerium für Bildung und Forschung (BMBF) geleitet.
In einer Zukunft, in der Maschinen, Produkte und Abläufe in der Industrie weitgehend digital vernetzt sein werden, werden die Unternehmen neue Technologien einsetzen, um die Prozesse weiter zu optimieren. Autonome Maschinen werden in einem dann digital vernetzten Umfeld gezielt gut einsetzbar sein. Inwiefern autonome Maschinen auch über die Industrie hinaus im Alltag Hand in Hand mit Menschen arbeiten werden, wird sich zeigen.
Gekennzeichnet ist die in den Medien auch als vierte industrielle Revolution bezeichnete Industrie 4.0 durch eine zunehmende digitale Vernetzung von Abläufen, Produkten und Maschinen in der Wirtschaft – über alle Branchen hinweg.
Durch die zunehmende, intelligent umgesetzte Digitalisierung können Abläufe effizienter gestaltet werden. Um sich erfolgreich am Markt zu halten und wettbewerbsfähig zu bleiben, spielt der Digitalisierungsgrad eines Unternehmens oft eine zentrale Rolle.
Das sind Technologien, die eine digitale Vernetzung von Maschinen oder Abläufen fördern. Je nach Branche gibt es ganz unterschiedliche Beispiele. Dazu gehören etwa cloud-basierte Internet-of-Things-Plattformen, auf denen selbstlernende Maschinen beziehungsweise Geräte miteinander vernetzt sind und über das Internet kommunizieren. Maschinen können dabei beispielsweise eigenständig darauf hinweisen, dass sie repariert werden müssen. Service-Roboter können Menschen unterstützen. Autonome Fahrzeuge können Produkte transportieren.
Einerseits bietet sie die Chance, effizienter zu arbeiten und sich im Wettbewerb Vorteile zu verschaffen. Andererseits gibt es auch Risiken. So müssen die neuen Technologien finanziert werden. Auch Cyberangriffe können zunehmen, potenziell mehr Schaden verursachen und es müssen Sicherheitsvorkehrungen getroffen und diese regelmäßig an den neusten technischen Stand angepasst werden.
Je nach Branche gibt es am Arbeitsplatz unterschiedliche Auswirkungen. Beispielsweise kann die zunehmende Digitalisierung der Abläufe je nach Arbeitsstelle dazu führen, dass Arbeitnehmerinnen und Arbeitnehmer ortsunabhängig – etwa auch aus dem Homeoffice – arbeiten können. Fachkräfte mit Industrie-4.0-Kompetenzen sind besonders gefragt. Die Bedeutung von allen Formen der Arbeit, die Maschinen ersetzen können, wird hingegen weiter abnehmen. Mitarbeiterinnen und Mitarbeiter müssen für neue Technologien geschult werden.